Expecting the Unexpected: How Contingency Planning can Save Your Build Project
By Mike Niezer, RA Ron Dick, AIA, LEED AP
May 1, 2024Post Tagged in
Starting a build project can be intimidating, even if you’ve had experience with it before.There are so many factors that go into a successful project, so where do you even begin? We sat down with two experts in the design field, Ron Dick (Founding Partner and Architect) and Mike Niezer (COO and Architect), to talk about everything you need to know about the entire process. They discussed what to do before you start a project, the three essential parts of a project, developing a contingency plan, and how to set a realistic schedule for your project.
|
![]() |
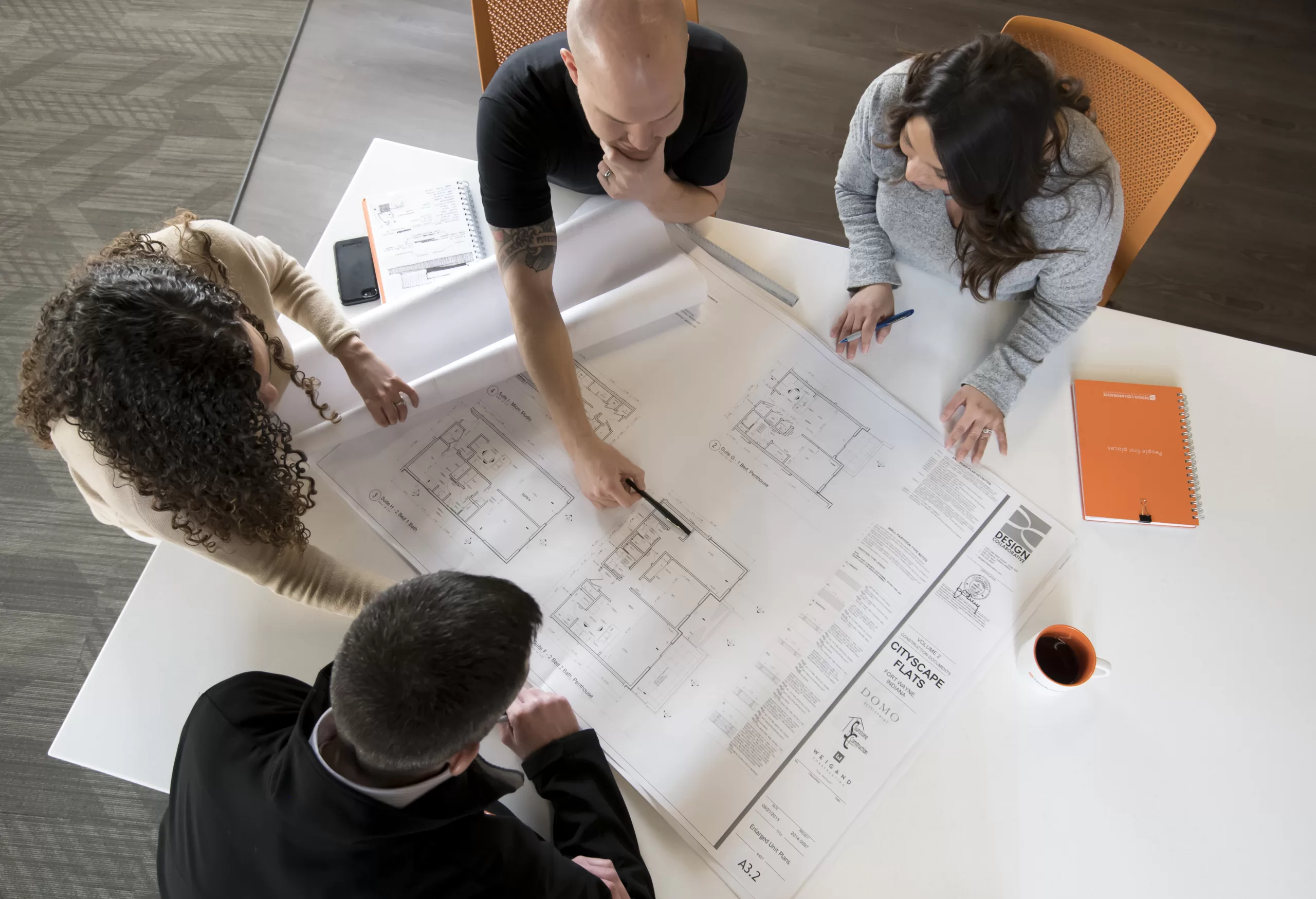
![]() |
Follow along with this series to hear what they have to say about each step in the process.In our first post, (Before you Start: Setting your Project up for Success) we began with why it’s critical for architecture and design teams to ask questions and really listen to the answers BEFORE getting started. We then reviewed the three essential parts of an overall project (Understanding the Three Essentials of a Successful Build Project: Quality, Cost, and Size). In this segment, we look at the importance of developing a contingency plan for your project. |
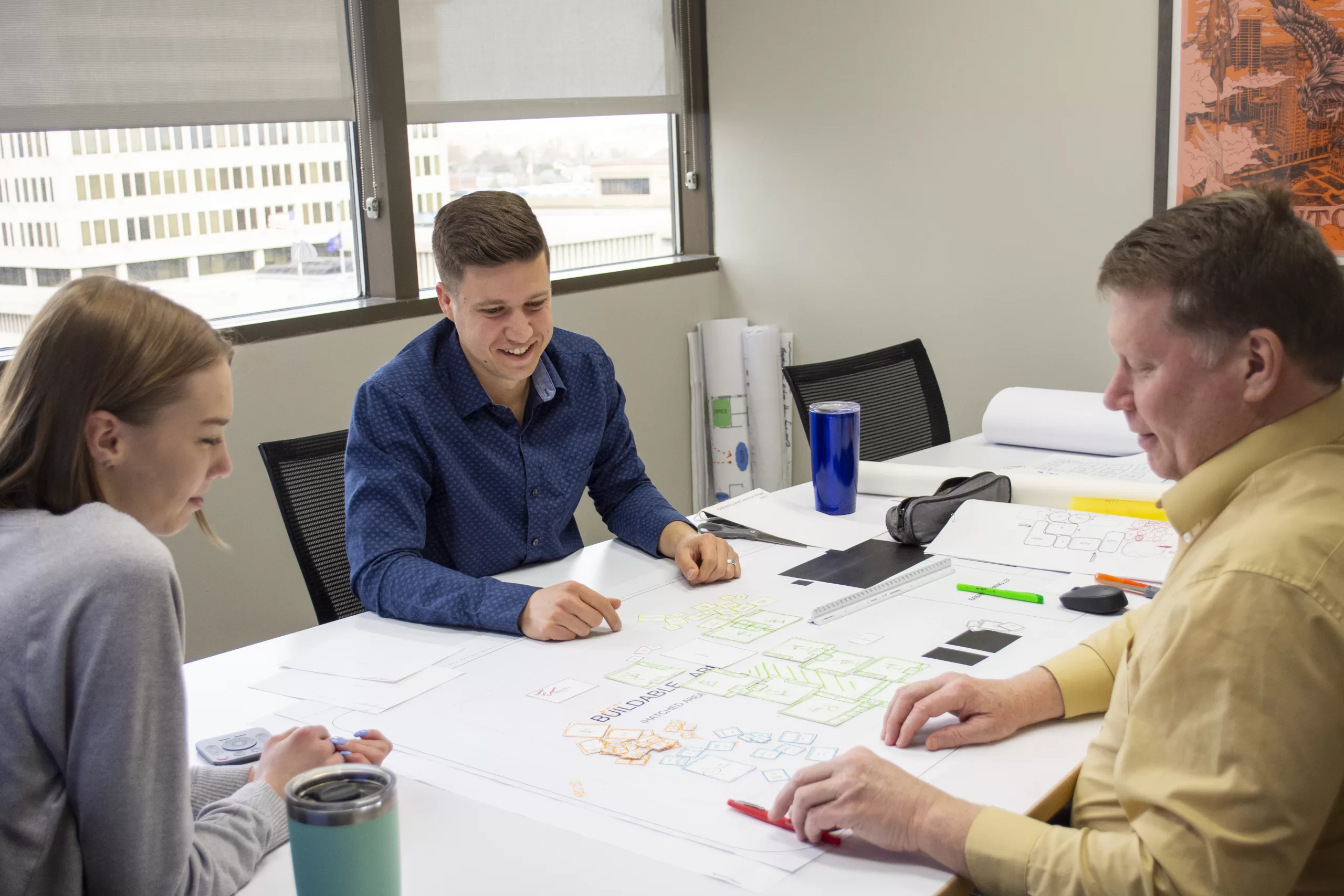
Mike Niezer: We know project cost is always important, every project has a budget.There are all kinds of different alternatives for decision points in the project, and our job is to help advise the client on good, better, and best options for as many of those decision points as possible. We spend a lot of time and effort in the design phases to make sure this all lines up, but there are all kinds of variables that impact cost, and sometimes those are things we can’t control. Market conditions, inflation, material escalation, labor shortages, exorbitant lead times, product discontinuation, and inclement weather, are some examples. The reality is, there is a change management component of design and construction that is just a part of the process. The expectation going into any project is that you’re going to run into a few of those.
|
![]() |
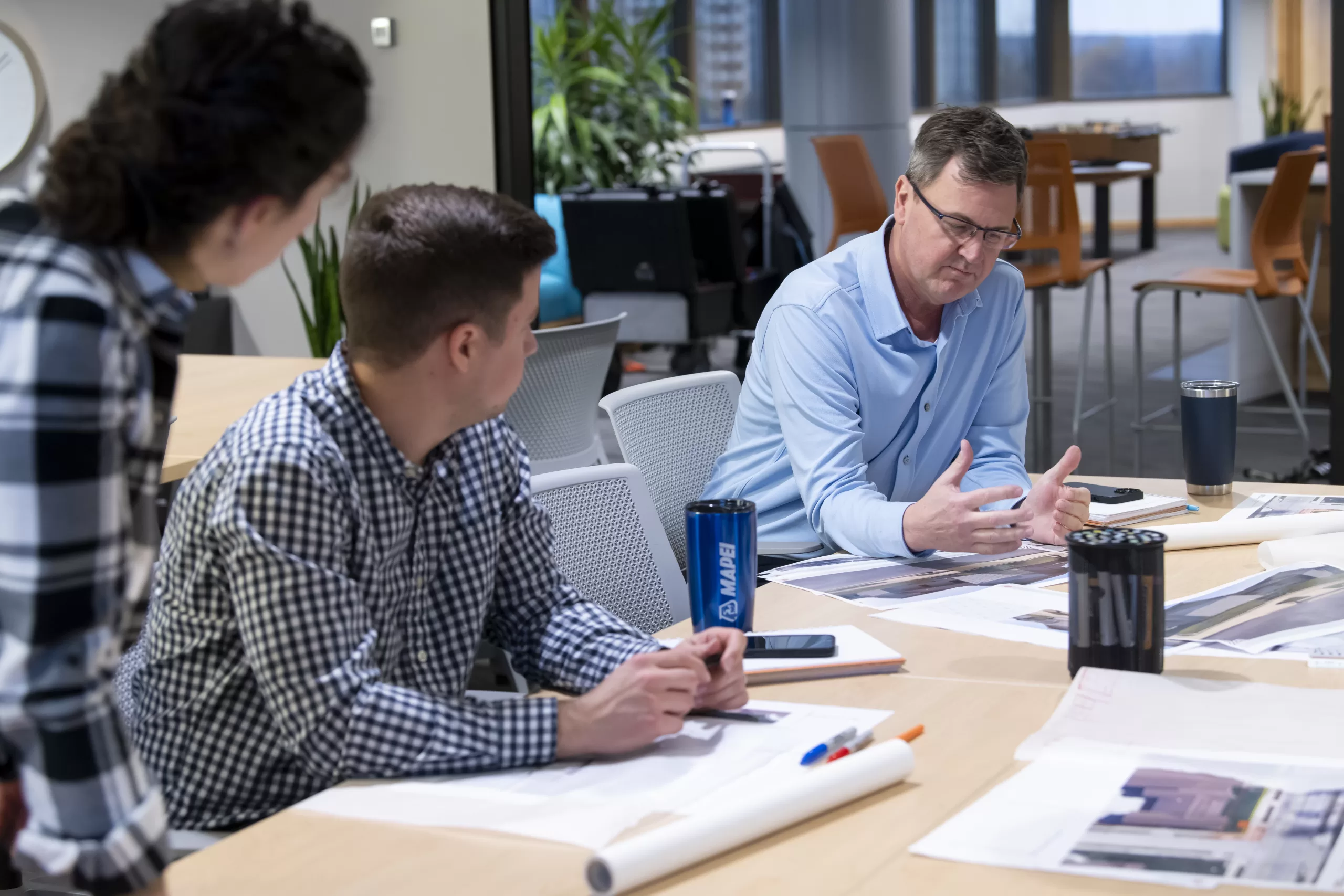
![]() |
Ron Dick: So with that said, how can we anticipate these changes and manage them in a good way?This is where we really advocate for establishing a contingency for the project, to protect the client from unexpected costs that may arise during the process. It’s really smart to budget for this in the design phase, and adjust that contingency as the design progresses and those early assumptions are confirmed into project criteria. Through the design process, you’re really trying to make those unknowns known, but even then there will always be surprises in the construction phase. If it’s a renovation project, for example, you may find something behind a wall that you didn’t know was going to be there. That’s why we advise clients include contingency costs in any project budget, to accommodate the unexpected. A contingency schedule isn’t a bad idea, either.
|
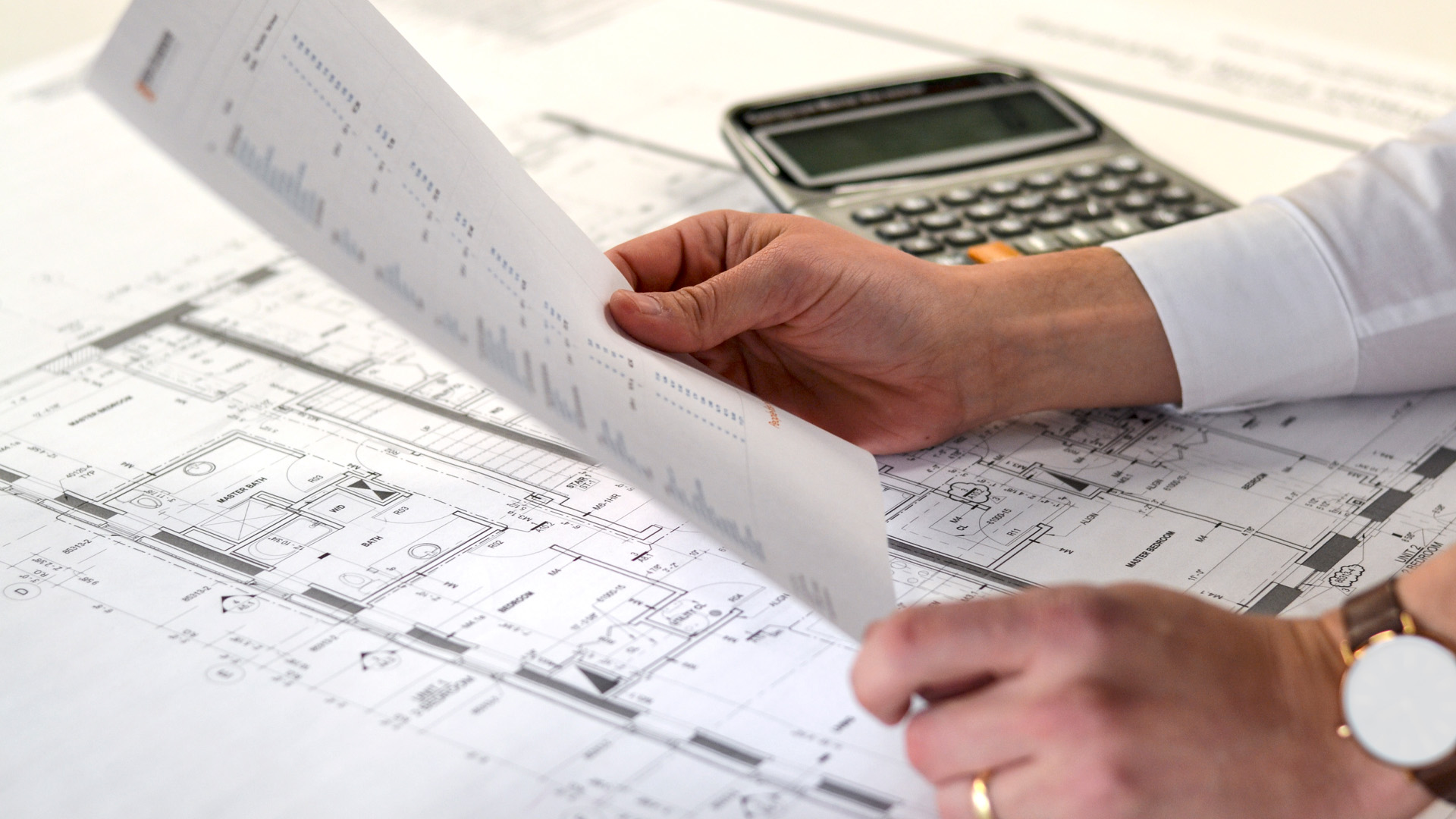
Mike Niezer: That’s exactly right.Big picture, we don’t know with certainty what those change factors will be, but contingency planning is one of the best ways to protect against unexpected changes, and still maintain the other non-cost related project goals as well. We don’t ever want our clients to feel like they have to sacrifice quality or program with an unexpected change – unfortunately sometimes that is the reality – but if we can help guard against that, the project is ultimately better for it. Bottom line is, it’s always wise to have a contingency plan. |
![]() |
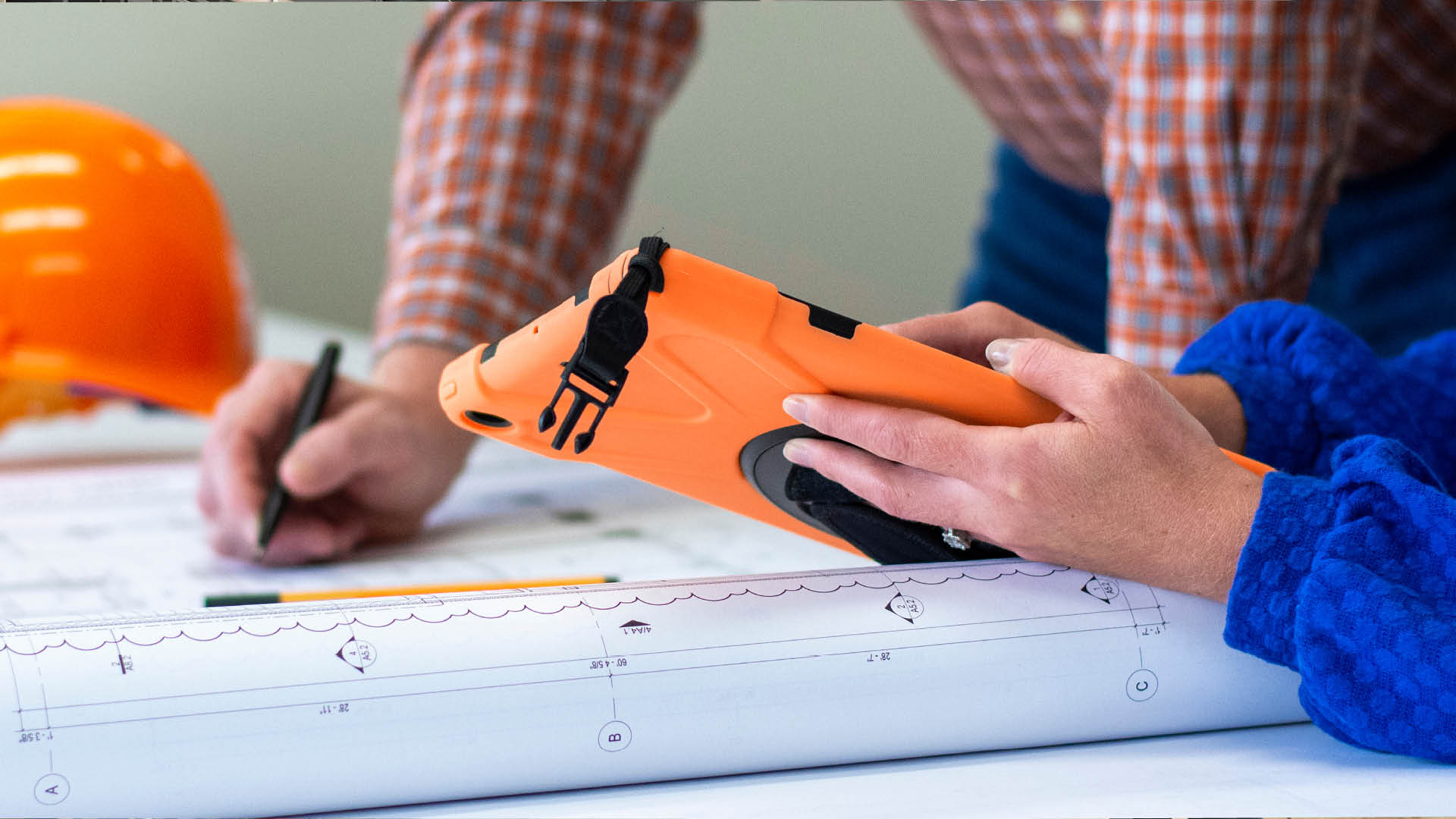
![]() |
Ron Dick: There’s this whole other side of soft costs, too.Furniture, fixtures, and equipment (FFE), A/V, artwork, and signage are some examples of things that sometimes get overlooked, but are obviously important to plan around. Some project types in particular can run pretty high with soft costs – healthcare, for instance, can have significant budgets for major medical equipment, technology, etc.
|
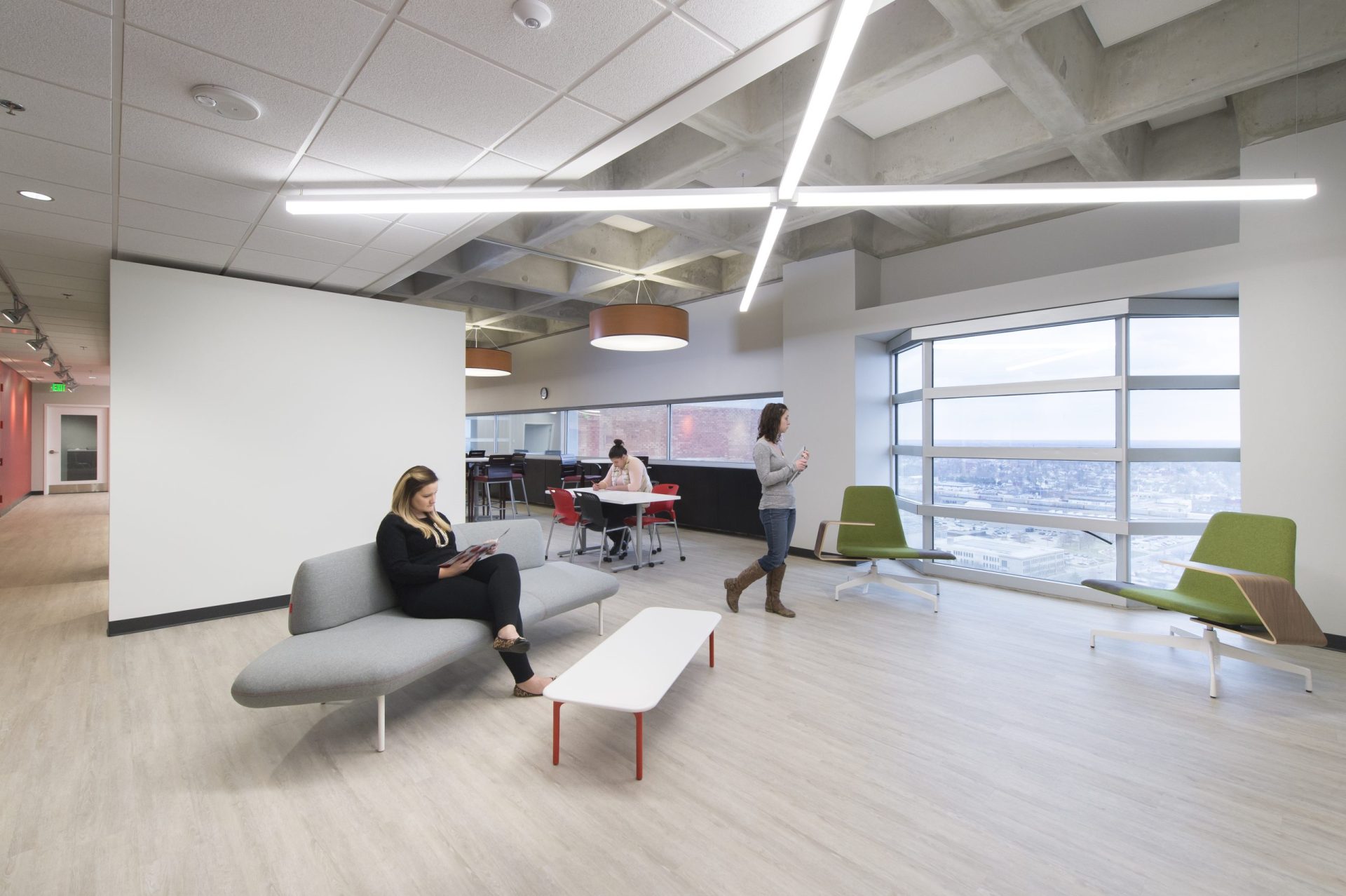
Mike Niezer: These soft cost examples should be budgeted for, but they’re usually a separate bucket from other “hard” construction costs that are included by the General Contractor.This isn’t to say that the Contractor won’t or doesn’t still coordinate their work around these other areas of work, but the responsibility to procure those elements and perform their installation is normally done by the Owner or delegated elsewhere. We’ve seen soft costs comprise anywhere from 15% to 30% of total construction cost, and it really just varies based on the type of project and specific requirements. Selecting the right design and construction partners can definitely help plan for these things in the budgeting phase to make sure the budget is inclusive of everything, not just construction costs. |
![]() |
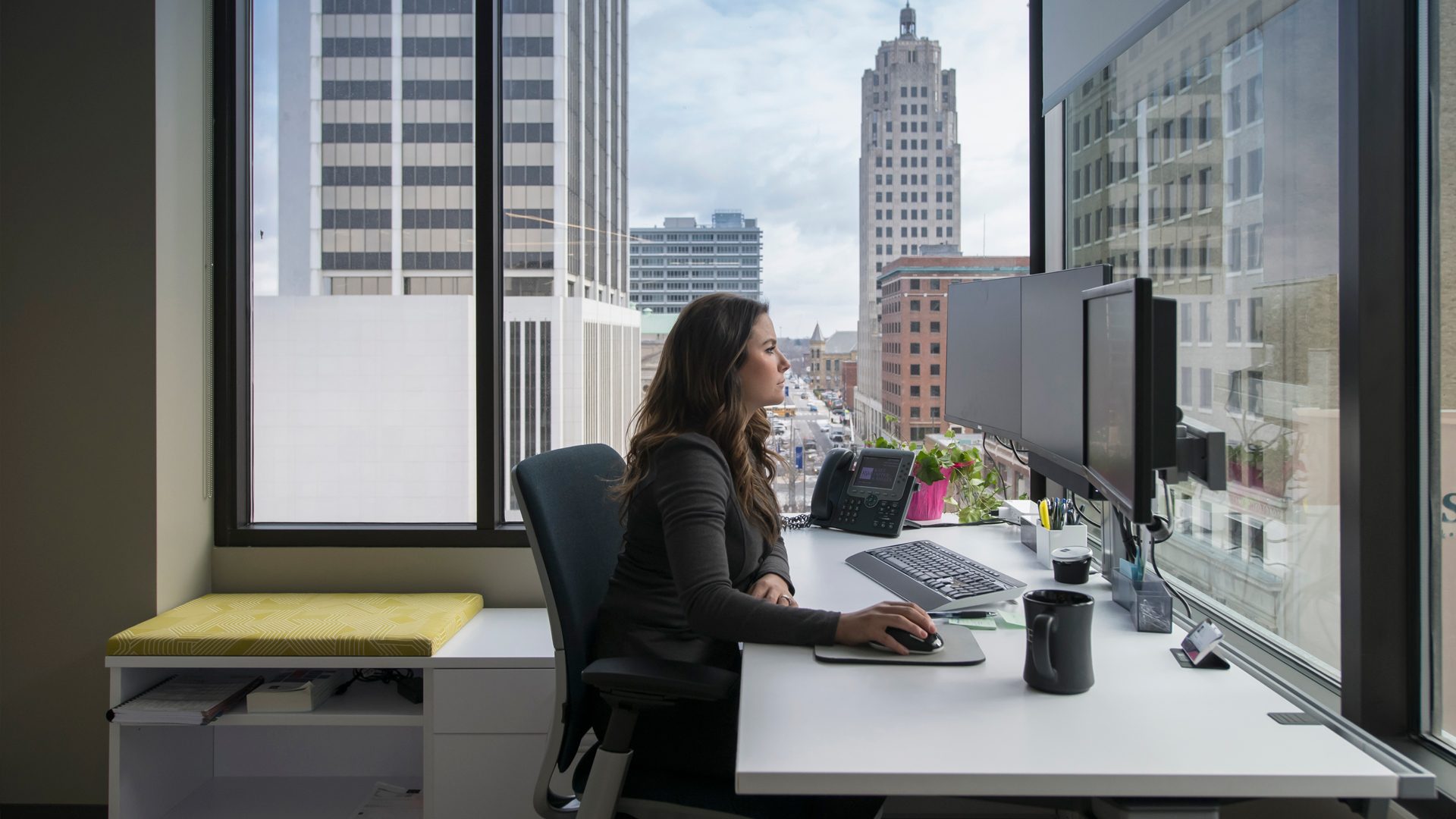